銑刀
此條目翻譯品質不佳。 (2019年6月27日) |
銑刀是通常用於銑床或加工機的切削工具,以執行銑削操作(有時在其他機床中)。它們通過其在機器內固定的進給率進行移除材料。
銑刀的特點
[編輯]
銑刀具有幾種形狀和許多尺寸。 還可以選擇塗層,以及螺旋角和切割面數量。
- 形狀:銑刀的幾種標準形狀在當今的工業中被使用,這在下面將更詳細地解釋。
- 排屑槽 / 刀刃:銑頭的凹槽是沿着切割器運行的深螺旋槽,而沿着凹槽邊緣的鋒利刀片被稱為刃。刃切割材料,並且該材料的切屑通過旋轉中的鑽頭推出排屑槽。每個排屑槽幾乎總是有一個刀刃,但是一些切割器每個排屑槽有兩個刀刃。[1] 通常,排屑槽和刀刃可以互換使用。 銑刀可能有一個到多個刀刃,2刃、3刃和4刃是最常見的。通常,刀刃具有的齒越多,其能夠更快地去除材料。因此,4齒刀可以比2齒切削刀的兩倍速度去除材料。
- 螺旋角:銑刀的槽紋幾乎總是螺旋形的。如果排屑槽是直的,整個刀刃會立即衝擊材料,造成振動,降低精度和表面質量。以一定角度設置排屑槽可以使刀刃逐漸進入材料,減少振動。通常,精加工刀具具有更高的螺旋角以得到更好的加工。
- 中心切割:有一些銑刀可以通過材料直線向下鑽,大部分銑刀是不能直線向下。這是因為刀具的刀刃不能一直到達終端的中心。但是,這些刀具可以以45度左右的角度向下切割。
- 粗加工或整理:不同類型的銑刀可用於切割大量材料,留下不良的表面光滑度(粗加工),或去除較少量的材料,但留下良好的表面光滑度(精加工)。粗加工刀具可以具有用於將材料碎屑破碎成更小片的鋸齒狀齒。這些刀刃留下了粗糙的表面。精加工刀具可以具有大量(4個或更多個)刀刃,用於小心地去除材料。然而,大量的槽紋幾乎沒有有效的切屑去除的餘地,因此它們不太適合去除大量的材料。
- 塗層:正確的工具塗層可以通過提高切割速度和刀具壽命以及改善表面光潔度對切割過程產生很大的影響。合成鑽石(PCD)是用於刀具的特殊硬塗層,必須承受高磨損。PCD塗層的工具可以比未塗覆的工具長達100倍。然而,塗層不能在高於600攝氏度的溫度或黑色金屬上使用。鋁加工的工具有時會被塗覆氮化鋁鈦。鋁是一種相對較粘的金屬,可以將其自身焊接到工具的牙齒上,使它們看起來鈍。然而,它傾向於不粘附TiAlN,允許該工具在鋁中使用更長時間。
- 柄:柄是刀具的圓柱形(非凹槽)部分,用於將其固定並定位在刀架中。柄可以是完全圓形的,並且通過摩擦保持,或者可以具有焊接平面,其中定位螺絲也稱為無頭螺絲在沒有工具滑動的情況下接觸以增加扭矩。直徑可能與工具的切割部分的直徑不同,因此可以由標準的工具夾保持。
選擇銑刀
[編輯]選擇銑刀不是一件簡單的工作。有很多變數,意見和理由需要考慮,但基本上師傅正在努力選擇一種能夠以最低成本將材料切割成所需規格的工具。工作的成本少部分來自於工具的價格,銑床所花費的時間以及師傅花費的時間的組合。通常,對於大量零件的工作和加工時間的日子,工具的成本是三個成本中最低的。
- 材料:高速鋼(HSS)銑刀是最便宜和壽命最短的銑刀。與常規高速鋼相比,含鈷高速鋼通常可以運行10%更快。硬質合金工具比鋼更昂貴,但持續時間更長可以運行得更快,從長遠來看證明更經濟。[來源請求] HSS工具完全適用於很多應用。從常規HSS到鈷HSS到碳化物的發展可以被認為是非常好的。使用高速主軸可能會排除HSS的使用。
- 直徑:較大的工具可以比較小的工具更快地去除材料,因此通常會選擇適合工作的最大可能的刀具。當銑削內部輪廓或凹入的外部輪廓時,直徑受內部曲線的大小限制。刀具的半徑必須小於或等於最小弧的半徑。
- 排屑槽:更多的槽紋允許更高的進給速率,因為每個排屑槽有較少的材料被去除。但由於核心直徑增加,切屑的空間較小,因此必須選擇平衡。
- 塗料:諸如氮化鈦等塗料也增加了初始成本,但減少了磨損並延長了刀具壽命。TiAlN塗層減少鋁對工具的粘附,減少並有時消除了潤滑的需要。
- 螺旋角:高螺旋角通常是軟金屬最好的,硬質或韌性金屬的螺旋角較低。
類型
[編輯]端銑刀
[編輯]
立銑刀(圖中的中間排)是在一端以及側面具有切削齒的那些刀具。立銑刀一詞通常用來指平底刀,而且還包括圓形刀具(稱為「球頭」)和圓角銑刀(簡稱「大鼻子」)或「 'torus')。 它們通常由高速鋼或硬質合金製成,並具有一個或多個凹槽。它們是立式磨機中最常用的工具。
粗加工立銑刀
[編輯]粗加工立銑刀快速清除大量物料。這種立銑刀使用在周邊切割的波浪形齒形。這些波浪形齒形成許多連續的切削刃,產生許多小的切屑,導致相對粗糙的表面光潔度。在切割過程中,多個齒與工件接觸減少顫動和振動。用銑削切削快速切削刀片有時被稱為銑削。
面銑刀
[編輯]
面銑刀,它們的形狀像一條管(但具有較厚的壁),其本體的周圍及側面具有刀刃。
使用銑刀
[編輯]碎片形成
[編輯]儘管有多種不同類型的銑刀,但是了解切屑的形成對於使用它們是至關重要的。當銑刀旋轉時,待切割的材料被送入其中,並且切割器的每個齒切掉一小塊材料。實現正確的碎片尺寸至關重要。該碎片的尺寸取決於幾個變量。
- 表面切割速度 (Vc)
- 這是刀具旋轉時每根牙齒穿過材料的速度。這是以公制國家/分鐘的米/秒或美國每分鐘錶面英尺(SFM)來衡量的。某些鋼的切割速度的典型值為10m/min至60m/min,鋁為100m/min和600m/min。這不應該與進給速率混淆。該值也稱為「切向速度」。
- 主軸轉速(S)
- 這是刀具的轉速,以每分鐘轉數(rpm)測量。 典型值為數百 rpm,高達數萬 rpm。
- 刀具直徑(D)
- 齒數(z)
- 每齒進給(Fz)
- 這是當每個齒旋轉時材料被送入刀具的距離。 這個值是牙齒最深切割的大小。
- 進料速率(F)
- 這是材料進給刀具的速度。典型值為 20mm/min 〜 5000mm/min。
- 切削深度
- 這是工具在待切割材料表面下的深度。這將是晶片生產的高度。通常,切割深度將小於或等於切割工具的直徑。
師傅需要三個值:S, F和深度 在決定如何使用新工具切割新材料時。 但是,他可能會被賦予價值 Vc和 Fz從工具製造商。 S和F可以從他們計算:
主軸轉速 | 進料速率 |
---|---|
從主軸速度S的公式來看,可以看出,較大的刀具需要較低的主軸轉速,而小型刀具可能會以高速運轉。 | 進料速率F的公式表明,增加S或z可以提供更高的進料速率。因此,師傅可以選擇具有最高數量的牙齒的工具,該刀具仍然可以應付切屑負荷。 |
逆向銑削與順向銑削
[編輯]
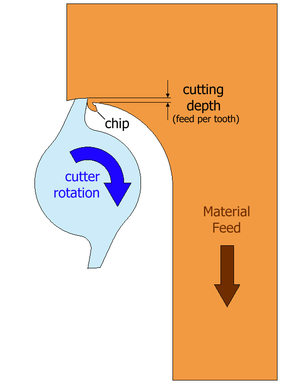
銑刀可以在兩個方向做切割,有時稱為逆向或上、順向或下。
- 逆向銑削(左):切削厚度從零厚度開始,並增加到最大值。切割在開始時如此輕巧,刀具不切割,但滑過材料表面,直到足夠的壓力被建立,牙齒突然咬傷並開始切割。這會使材料變形(圖中的點A,左側)、並使工具變鈍在材料上留下不好的表面。
- 順向銑削(右):每個刀刃在一定的位置接合材料,並且切割的寬度從最大值開始減小到零。晶片設置在切割器後面,導致切屑更容易拆卸。刀刃不會磨擦材料,因此刀具壽命可能會更長。然而,爬升可以對機器施加較大的負載,但是不建議用於較舊的銑床或機器。
刀具位置(刀具半徑補償)
[編輯]刀具位置是為了實現所需工件輪廓(幾何形狀)而定位刀具的位置,因為刀具尺寸不為零。最常見的示例是刀頭半徑補償(CRC),其中刀具的中心線將通過「距離」等於刀具半徑的向量偏離目標位置,並且其「方向」為由常規銑削與爬坡 左/右,爬升/常規,上/下區別統治。
在G-code的大多數實現中,控制CRC(G40取消,G41左/爬,G42右/常規)是G40至G42。每個刀具的半徑值由CNC操作員或機械師輸入到偏移量寄存器中,然後在生產過程中對其進行調整,以使成品尺寸保持在公差範圍內。使用球磨機進行3軸,4軸或5軸銑削的3D輪廓的切割器位置由CAM軟件輕鬆處理,而不是手動編程。
通常,通過針對特定CNC控制模型量身定製的後處理器程序將CAM向量輸出後處理為G代碼。一些後期型CNC控制器直接接受向量輸出,並在內部進行伺服輸入的轉換。
清除切屑
[編輯]銑刀的另一個重要品質是考慮切削加工產生的切屑的能力。如果切屑沒有像產生的那樣快速移動,則凹槽會阻塞並有效地防止刀具切割,導致振動,刀具磨損和過熱。影響切屑消除的幾個因素,包括凹槽的深度和角度,切屑的尺寸和形狀,冷卻劑的流動以及周圍的材料。可能很難預測,但是一個好的機械師會注意切屑堆積,並且如果觀察到的話調整銑削條件。
參考文獻
[編輯]- ^ Rapid Traverse: More Teeth Per Flute 互聯網檔案館的存檔,存檔日期2007-09-27.
參考書目
[編輯]- De Vries, D., Milling machines and milling practice: a practical manual for the use of manufacturers, engineering students and practical men, London: E. & F.N. Spon, 1910. Coedition, New York, Spon & Chamberlain, 1910.
- Template:Roe1916
- Woodbury, Robert S., History of the Milling Machine. In Studies in the History of Machine Tools, Cambridge, Massachusetts, USA, and London, England: MIT Press, 1972 [1960], ISBN 978-0-262-73033-4, LCCN 72006354. First published alone as a monograph in 1960.